Mechanical Design Portfolio
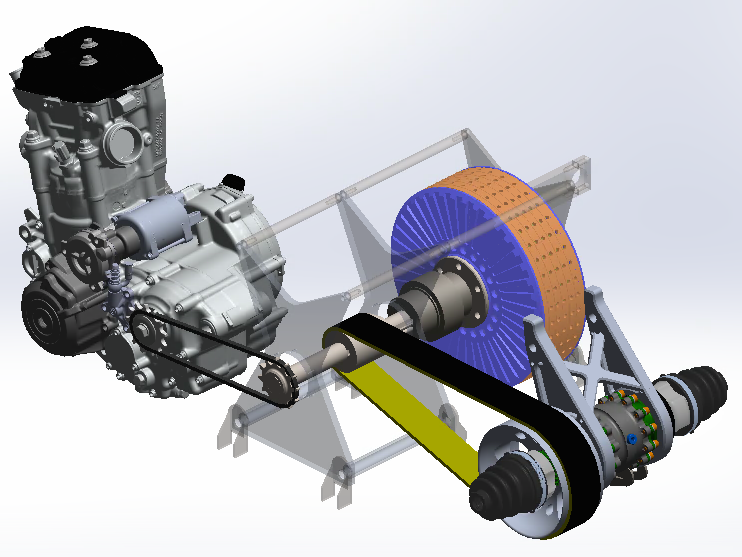
Motor, mounted on support plates, coupled to the internal combustion engine and driving the differential.

One of two mirror-image battery packs to be mounted on either side of the chassis. The exterior of the container is aluminum, lined with mica for insulation. The batteries sit in a noryl receptacle and are held in place vertically by noryl ribs on the lid (not shown).
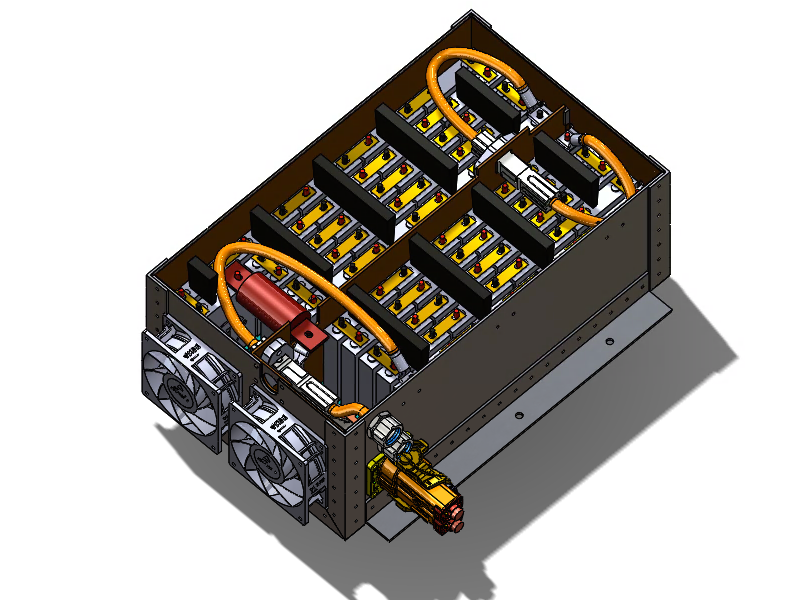
SolidWorks model showing the battery layout and accumulator container.
Electric Powertrain
For my capstone design project, I worked in a team of 6 to design and manufacture an electric powertrain for Dartmouth's Formula Hybrid racecar. This consisted of an accumulator of 84 3V LI batteries bussed together in series and split between two battery packs; a battery management system monitoring the voltage of each cell, the temperature throughout the pack, and implementing active cell balancing; a motor coupled to the internal combustion engine and providing torque to the differential; a motor controller; a pre-charge circuit and charge port; and a cooling system, liquid for the motor and motor controller, and air for the battery containers.
My focus on the project was first on the coupling of the motor to the engine, including mounting the motor and coupling components to the chassis, and creating an integration plan for the Formula Hybrid team to install our powertrain, including finite element analysis and failure modes and effects analysis for key components. Secondly, I created CAD for the battery housing and was the primary manufacturer of the container, using 2-axis mills for the aluminum exterior and mica insulation, and CNC mill programs for the noryl plastic interior.